Modern technological processes of obtaining cast products and structures of responsible purpose from aluminum, ferrous carbon and heat-resistant alloys
Keywords:
aluminum alloys, Al-Mg-Sc system, alloying, chrome, REM, deformation treatment, structure, structural strength, corrosion resistance, damage, vacuum magnetohydrodynamic mixer, continuous ingot casting machine, modification, heat-resistant corrosion-resistant nickel alloys, gas turbine engine blades, directional crystallization, composite castings, cast reinforced structures, iron-carbon alloys, gasification model casting, chromium-nickel alloys, austenite, hardness, wear rate, wear resistance index, deformable aluminum alloys, vacuum magnetohydrodynamic complex, heat-resistant alloy, gas turbine engine, turbine blade, continuously cast aluminum ingots, iron-carbon alloyscasting according to gasifying models, thermal destruction of polystyrene, physical and mechanical properties of cast structures, influence of pressure on metalAbstract
The chapter presents the results of scientific research and development of new highly efficient foundry technologies for the production of cast and composite structural materials and products with high operational characteristics from alloyed and reinforced aluminum, iron-carbon and heat-resistant alloys.
The latest technological processes for the production of cast construction materials from aluminum alloys combine the influence of electromagnetic, plasma kinetic, centrifugal actions on metal systems in a vacuum, which makes it possible to obtain large-sized custom products for the space and atomic industries by the casting method.
The results of theoretical and experimental studies using the method of jet gas cooling of molds in a vacuum for obtaining blades of gas turbine engines (GTE) with a regular directional casting structure are given.
Promising technologies for obtaining cast iron and steel reinforced structures based on gasification patterns by liquid-phase combination of system components have been developed. The results of the study of the thermal state of the reinforced casting by the methods of mathematical and computer modeling are presented, the physical model of mass and heat transfer of reinforcing elements and matrix alloy during the formation of the structure and properties of cast reinforced structures is presented.
The works carried out by the authors at the Physical and Technological Institute of Metals and Alloys of the National Academy of Sciences of Ukraine are of high scientific and practical importance for the development of foundry production and will be useful for foundry product manufacturers, scientific and scientific-pedagogical workers in the specialty "Metallurgy" (Foundry production).
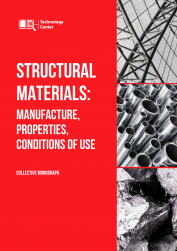
STRUCTURAL MATERIALS: MANUFACTURE, PROPERTIES, CONDITIONS OF USE