Cast and deformation strengthened alloys of the Al-Mg-Sc system
Keywords:
aluminum alloys, Al-Mg-Sc system, alloying, chrome, REM, deformation treatment, structure, structural strength, corrosion resistance, damage, vacuum magnetohydrodynamic mixer, continuous ingot casting machine, modification, heat-resistant corrosion-resistant nickel alloys, gas turbine engine blades, directional crystallization, composite castings, cast reinforced structures, iron-carbon alloys, gasification model casting, chromium-nickel alloys, austenite, hardness, wear rate, wear resistance index, deformable aluminum alloys, vacuum magnetohydrodynamic complex, heat-resistant alloy, gas turbine engine, turbine blade, continuously cast aluminum ingots, iron-carbon alloyscasting according to gasifying models, thermal destruction of polystyrene, physical and mechanical properties of cast structures, influence of pressure on metalAbstract
The effect of reducing the magnesium content and doping with scandium, zirconium, manganese, chromium, and rare-earth metals on the structure, phase composition, strength, plasticity, and crack resistance, as well as the potential and corrosion current of alloys of the Al-Mg and Al-Mg-Sc systems obtained using magnetohydrodynamic foundry was investigated. Installation a positive effect of reducing the magnesium content, replacing manganese with chromium, and alloying with lanthanum in alloys of the Al-Mg-Sc system in the cast state and after deformation processing (extrusion, pressing, and rolling) was established. It is shown that due to dispersion strengthening by secondary intermetallics of chromium and lanthanum, this alloy in the cast state after homogenization is superior in strength to the well-known alloys of grades 1570 and 1545. After hot and cold rolling, it is not inferior to these alloys in terms of strength and plasticity, but has higher corrosion resistance characteristics. It was found that in terms of structural strength, which is comprehensively determined by the characteristics of strength and cyclic crack resistance, such alloys are superior to the well-known Al-Mg-Sc, Al-Mg and Al-Cu-Mg systems. The results of modeling the stress-strain state and damage of strips of different thicknesses during hot isothermal pressing are presented. The temperature-force parameters of the process and the geometry of the pressed strip are set to obtain its minimal damage.
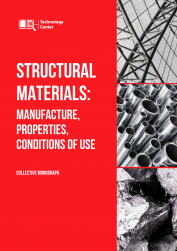
STRUCTURAL MATERIALS: MANUFACTURE, PROPERTIES, CONDITIONS OF USE